Ronnie Sullivan
Member
I have a customer that has a huge centrifugal hydro dryer.
They put up to 10 ton of wet yarn into it and 'spin dry' it.
It looks a bit like this one but much much bigger.
I retro-automated it a long time ago, so it has 'been my baby' ever since.
The operatives (who are paid from the neck down) don't care if they put the load in unbalanced (even though they are told spread the product evenly) and when 10 ton gets a lick-on the whole thing shakes like (as the engineer put it so eloquently) like it's trying to climb out of its pit.
It came with an anti-vibration unit - a very imaginative ball bearing sat in a groove that is thrown out of the grove onto a micro switch when it vibrates.
The trouble with that is - setting it up is almost impossible. Too fine and it trips the switch on nearly every start up. Too coarse and it either doesnt work or hits the switch on every revolution with mild vibration
I tried programming it out of the start up but it's my opinion that it is not good enough.
It came to a head a while back when the main shaft sheared and it was out of action for 2 weeks while it was repaired. It was probably due to, in part excessive vibration over a long period.
Does anyone know of anti-vibration switches that are digital or analog that can be monitored throughout the running of the machine?
A normal run of this machine would be as follows. On start up it has a 30 second ramp up time. it starts to gently lurch at about 15 seconds (this is ok)
As it gets faster it settles down but can still vibrate about 1cm 1/2 inch off center (this is still acceptable, it has massive springs to take this up)
If the load is very unbalanced - this vibration can increase to 2 to 4 inch and that's when I want to stop it................hmmm any suggestions?
They put up to 10 ton of wet yarn into it and 'spin dry' it.
It looks a bit like this one but much much bigger.
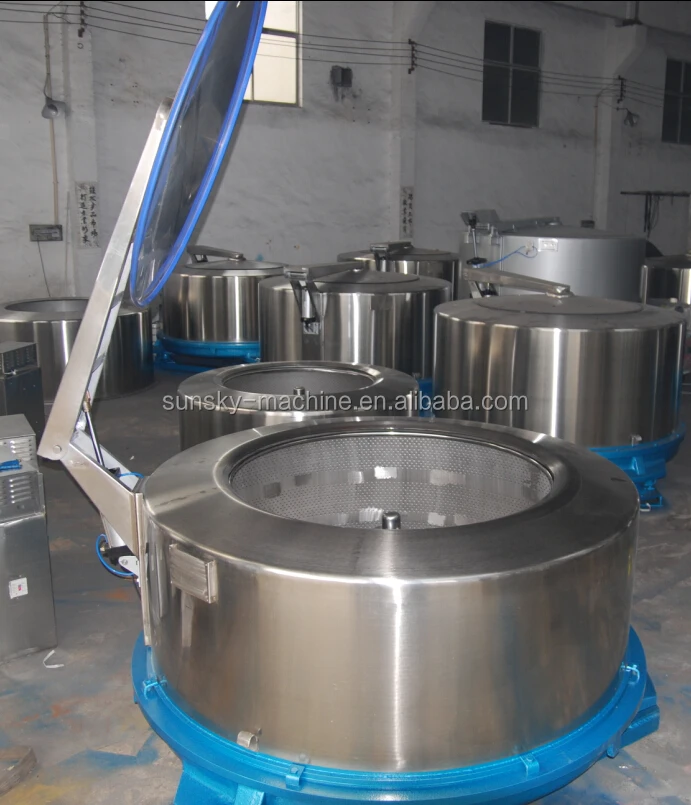
I retro-automated it a long time ago, so it has 'been my baby' ever since.
The operatives (who are paid from the neck down) don't care if they put the load in unbalanced (even though they are told spread the product evenly) and when 10 ton gets a lick-on the whole thing shakes like (as the engineer put it so eloquently) like it's trying to climb out of its pit.
It came with an anti-vibration unit - a very imaginative ball bearing sat in a groove that is thrown out of the grove onto a micro switch when it vibrates.
The trouble with that is - setting it up is almost impossible. Too fine and it trips the switch on nearly every start up. Too coarse and it either doesnt work or hits the switch on every revolution with mild vibration
I tried programming it out of the start up but it's my opinion that it is not good enough.
It came to a head a while back when the main shaft sheared and it was out of action for 2 weeks while it was repaired. It was probably due to, in part excessive vibration over a long period.
Does anyone know of anti-vibration switches that are digital or analog that can be monitored throughout the running of the machine?
A normal run of this machine would be as follows. On start up it has a 30 second ramp up time. it starts to gently lurch at about 15 seconds (this is ok)
As it gets faster it settles down but can still vibrate about 1cm 1/2 inch off center (this is still acceptable, it has massive springs to take this up)
If the load is very unbalanced - this vibration can increase to 2 to 4 inch and that's when I want to stop it................hmmm any suggestions?